Manufacturing today is at a crossroads. With increasing pressure to boost productivity, ensure quality, and maintain regulatory compliance, downtime and process bottlenecks are costly realities.
In fact, unplanned downtime in manufacturing can cost companies up to $260,000 per hour on average, according to industry studies. This makes efficient incident resolution not just a competitive advantage, but a necessity.
ServiceNow’s platform is uniquely positioned to address these challenges by automating incident management and streamlining shop floor operations. From reducing production bottlenecks to improving quality control and compliance, manufacturers are leveraging ServiceNow to transform their workflows, reduce operational risk, and accelerate time to resolution.
In this blog, we will dive deep into how ServiceNow can revolutionize manufacturing operations with real-world use cases, practical strategies, and a clear blueprint for success.
The Real Impact of Production Bottlenecks
Production delays do more than disrupt schedules—they create a domino effect across the supply chain. Idle machines, waiting operators, and missed delivery windows all eat into efficiency and customer satisfaction.
In sectors like automotive or pharmaceuticals, even brief interruptions can trigger quality issues, regulatory headaches, or lost revenue. Yet, many shop floors still depend on manual processes and siloed systems to track and resolve incidents.
ServiceNow helps manufacturers tackle this by automating issue detection and resolution workflows. It ensures that incidents are logged instantly, routed to the right team, and resolved quickly, with full traceability. This minimizes repeat issues, reduces operational stress, and brings much-needed agility to production environments.
The Solution – ServiceNow for Manufacturing
Manual incident resolution simply can’t keep up with the pace of modern manufacturing. ServiceNow offers a smarter alternative, automated workflows that bring structure, speed, and visibility to shop floor issue management.
Manual tracking and delayed responses have no place in today’s high-speed manufacturing environment. ServiceNow delivers a unified platform that brings automation, visibility, and control to shop floor operations—driving real impact from the first incident to long-term optimization.
With ServiceNow for manufacturing, you can:
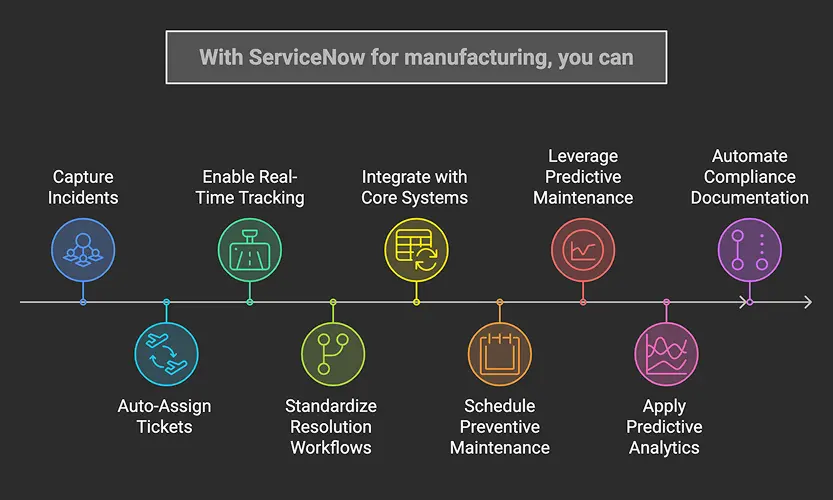
- Capture incidents automatically through IoT alerts, operator logs, or ERP/MES integration
- Auto-assign tickets based on asset type, severity, and team availability
- Enable real-time tracking with dashboards, SLAs, and escalation paths
- Standardize resolution workflows with role-based guidance and digital SOPs
- Integrate with core systems (like SAP, Oracle, MES) to sync production data and reduce manual input
- Schedule preventive maintenance and reduce reactive fixes through maintenance calendars
- Leverage predictive maintenance by analyzing equipment behavior trends
- Apply predictive analytics to detect patterns, anticipate issues, and optimize resource allocation
- Automate compliance documentation for audits, quality checks, and regulatory reporting
By eliminating fragmented responses and enabling intelligent decision-making, ServiceNow transforms incident resolution into a streamlined, proactive process. The result? Fewer bottlenecks, faster recoveries, and a production floor that runs smarter, not harder.
Real-World Use Cases – ServiceNow for Manufacturing in Action
Use Case 1 – Machine Downtime Escalations
Problem :-
A global automotive parts manufacturer faced frequent CNC machine breakdowns. Operators logged issues on paper, and maintenance response times varied wildly. Production delays became routine, and downtime reporting lacked transparency.
Solution :-
ServiceNow is integrated with their MES and IoT sensors to automatically detect anomalies and create incident tickets. Rules-based workflows routed tasks to the right maintenance teams with defined SLAs. Notifications and dashboards kept supervisors informed in real time.
Result :-
Machine downtime was reduced by 38% in the first quarter. Maintenance response times improved by 50%, and issue logging became fully traceable. Repeat failures dropped significantly due to root-cause visibility.
Use Case 2 – Compliance Risk in Regulated Manufacturing
Problem :-
A pharmaceutical manufacturing unit struggled to keep audit-ready maintenance logs. Compliance violations occurred due to missing records and delayed corrective actions on equipment failures.
Solution :-
ServiceNow enabled digital SOPs and automated logging of incidents and maintenance activities. Preventive maintenance schedules were integrated into daily operations, and alerts were triggered for overdue actions.
Result :-
Audit preparation time decreased by 60%. The company passed two regulatory inspections without findings. Teams no longer scrambled to locate documentation—it was all available, real-time, in the CMDB.
Use Case 3 – Inefficient Shop Floor Incident Reporting
Problem :-
Operators in a consumer electronics factory reported issues via calls and handwritten notes. There was no visibility for supervisors, leading to delays, duplicate tickets, and inconsistent resolution.
Solution :-
ServiceNow’s mobile-friendly portal allowed operators to log issues instantly using tablets stationed across the floor. Each report triggered automated categorization and task assignment, ensuring accountability.
Result :-
First-response times improved by 45%. Duplication of reports dropped to near-zero. Supervisors gained real-time visibility into open incidents and team workloads, leading to better shift planning.
Also Reads :-
Ready to Eliminate Bottlenecks for Good?
Production delays aren’t just costly—they’re avoidable. By replacing manual tracking with automated, intelligent workflows, manufacturers can finally gain control over incident resolution and operational efficiency.
ServiceNow isn’t just an IT platform—it’s a manufacturing enabler. From predictive maintenance to compliance automation, it transforms how your shop floor reacts, recovers, and grows.
If you’re ready to modernize your operations and bring real-time visibility to your factory floor, now is the time to act.
Download Our CMDB Readiness Blueprint
Want to ensure your configuration data supports automation and incident resolution at scale? Get our step-by-step CMDB readiness checklist and implementation guide.