Introduction – The True Cost of Unplanned Downtime
Unplanned downtime in manufacturing is more than an inconvenience—it’s a silent profit killer.
According to Deloitte, manufacturers lose an estimated $50 billion annually due to unexpected equipment failures. For global enterprises, a single hour of unplanned downtime can cost upwards of $100,000, including production losses, labor costs, penalties, and damaged customer trust.
The traditional break-fix maintenance model is reactive. It doesn’t give IT teams visibility, and by the time an issue is detected, the damage is already done.
This is where ServiceNow Predictive Maintenance in manufacturing becomes a game-changer. It equips Manufacturing IT Heads to automate and orchestrate proactive maintenance using real-time data, reducing costly downtime by up to 40%.
The Core Problem: Why Downtime Persists in Modern Plants
While modern production lines are more connected than ever, data fragmentation and operational silos remain a barrier. Here are the core challenges:
- Lack of machine-level visibility – Critical assets are not monitored in real-time.
- Delayed incident reporting – Frontline workers often spot problems after the failure.
- No centralized platform – Maintenance requests are scattered across systems or spreadsheets.
- Reactive response – Maintenance teams spend more time reacting than planning.
In many facilities, the maintenance process is still manual, disconnected from operational technology (OT) and lacking any workflow automation.
The result?
High Mean Time To Repair (MTTR), low First-Time Fix Rates (FTFR), and constant production disruption.
The ServiceNow Advantage – A Unified Platform for Smart Maintenance
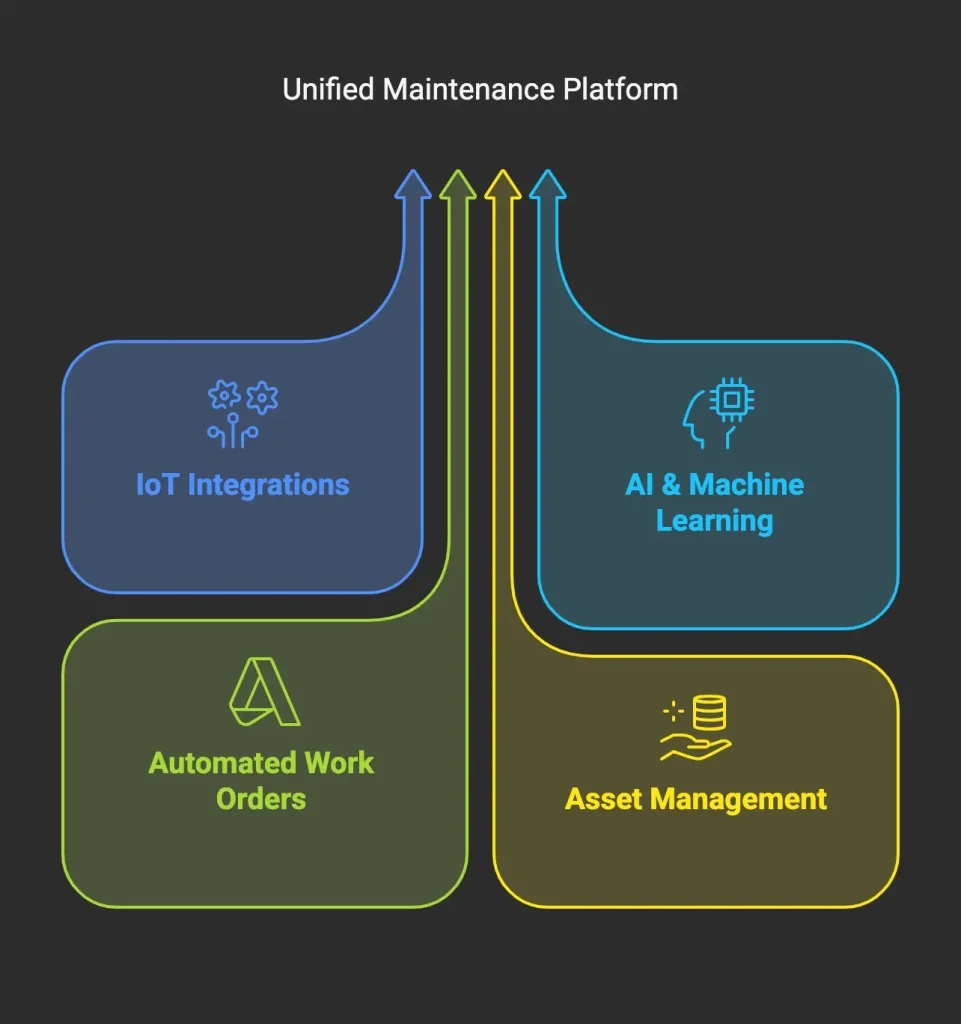
Real-Time Condition Monitoring with IoT Integrations
ServiceNow integrates with your PLC/SCADA systems and IoT sensors via its OT Management capabilities. This connection enables continuous asset monitoring.
Example:
A Tier-1 aerospace component manufacturer uses vibration and temperature sensors on CNC machines. Through ServiceNow, anomalies in RPM and temperature trigger an alert before a bearing fails, automatically initiating a maintenance request.
This preemptive signal allows maintenance teams to act before downtime occurs.
Predictive Maintenance via AI & Machine Learning
ServiceNow’s predictive engine uses historical failure data to build failure models and predict the probability of asset breakdowns. It takes into account:
- Equipment usage patterns
- Environmental conditions
- Past maintenance history
- Performance degradation trends
Example:
At an electronics assembly unit, ML models flagged a recurring failure pattern in soldering machines that wasn’t visible through routine checks. The prediction allowed the plant to pre-schedule part replacement, avoiding a three-day production delay.
Automated Work Order Generation and Technician Dispatch
Once an issue is detected or predicted, ServiceNow for manufacturing generates work orders automatically with zero manual effort. It selects the right technician based on availability, proximity, and skill match.
Technicians are notified via the ServiceNow FSM mobile app, complete with asset history, parts checklist, and resolution steps.
This level of workflow automation in manufacturing accelerates MTTR and improves team efficiency.
Integrated Asset Management and Spare Part Tracking
Through ServiceNow Asset Management, manufacturers can:
- Link spare parts to specific asset types
- Track part consumption rates
- Predict when inventory will need replenishment
- Avoid emergency procurement
Example:
An industrial valve manufacturing company reduced part-related delays by 22% by integrating its ServiceNow platform with spare part vendors. Procurement was triggered automatically based on predictive usage.
Real-World Benefits – What Manufacturers Are Reporting
Manufacturers who’ve adopted ServiceNow predictive maintenance workflows report the following:
Benefit | % Improvement |
---|---|
Downtime Reduction | 30–40% |
Maintenance Cost Savings | 20–30% |
MTTR Improvement | 25% |
Technician Productivity | 18–22% |
Equipment Uptime | 30% |
These outcomes are based on operational metrics from ServiceNow implementations in Tier 1 and Tier 2 manufacturing environments.
Strategic Value for IT Heads in Manufacturing
Manufacturing IT Heads are no longer infrastructure managers—they are transformation leaders.
By owning the predictive maintenance initiative, they can:
- Establish IT as a revenue enabler
- Lead OT/IT convergence
- Justify technology ROI using measurable KPIs
- Enable cross-functional coordination between production, quality, and maintenance teams
Key Metrics to Track in Your Predictive Maintenance Journey
Use Performance Analytics in ServiceNow to track these KPIs weekly:
Metric | Why It Matters |
---|---|
Mean Time Between Failures (MTBF) | Indicates equipment reliability |
Mean Time To Repair (MTTR) | Measures repair efficiency |
First-Time Fix Rate | Gauge technician effectiveness |
Unplanned Downtime Hours | Core cost metric |
SLA Compliance Rate | Service delivery accuracy |
When these are tracked and improved, CSAT scores from internal stakeholders also increase, which is critical in internal IT success metrics.
ServiceNow Use Cases in Manufacturing
Maintenance of Rotating Machinery
- Challenge – Sudden bearing failures
- Solution – Vibration sensors + AI modeling + proactive service
- Impact – Downtime reduced from 6 hours/month to under 1 hour/month
Cleanroom Air Handling Units
- Challenge – Dust levels triggering batch spoilage
- Solution – Predictive HVAC maintenance workflow with environmental sensors integrated with ServiceNow
- Impact: 100% batch compliance, reduced rework
Remote Equipment Monitoring
- Challenge: Off-site plants with no 24/7 engineer
- Solution: Real-time alerts to ServiceNow integrated with monitoring tools, auto-dispatch of mobile crew
- Impact: Reduced outage reaction time by 70%
Building Your Predictive Maintenance Roadmap with LMTEQ’s ServiceNow Solution
Here’s a phased approach you can follow:
- Discovery & Planning
- Identify high-priority assets
- Conduct a data readiness assessment
- Engage a ServiceNow partner such as LMTEQ for workflow planning
- Pilot Rollout
- Implement predictive maintenance for the top 3–5 assets
- Track performance for 30–60 days
- Full-Scale Integration
- Integrate with CMMS, ERP, SCADA
- Extend workflows to spare part vendors
- Continuous Optimization
- Add AI/ML predictive layers
- Build real-time KPI dashboards
- Scale to enterprise level across multiple plants
Final Word – Reduce Downtime. Boost Profits. Start Now.
If you’re a Manufacturing IT Head who wants to turn reactive maintenance into predictive value creation, ServiceNow is your path forward.
- Get proactive with ServiceNow Predictive Maintenance
- Build connected workflows across operations and maintenance
- Cut downtime by up to 40%, starting in just one quarter
Build Operational Resilience. Cut Downtime. Stay Ahead.
Don’t just react to problems — anticipate and prevent them.
ServiceNow is helping manufacturers achieve 40% less downtime through smarter, more resilient operations.
Download Our Free Whitepaper – Operational Resilience in Manufacturing with ServiceNow
What you’ll get:
- Real-world frameworks for building resilient shop floors
- How to align predictive maintenance with enterprise risk strategies
- Steps to modernize operations without disrupting production
Or you can contact our team for a personalized ServiceNow Consultation
Frequently Asked Questions
1. What is predictive maintenance in the manufacturing industry?
Predictive maintenance is a proactive approach that uses real-time data, analytics, and machine learning to monitor equipment health and predict when a machine is likely to fail. In manufacturing, it helps reduce unplanned downtime, extend asset life, and optimize maintenance scheduling, leading to increased productivity and cost savings.
2. What is the role of AI in predictive maintenance for manufacturing?
AI enables predictive maintenance by analyzing large volumes of sensor and machine data to identify patterns and anomalies that humans might miss. It can forecast potential failures, recommend optimal maintenance windows, and automate alerts, allowing manufacturing teams to act before breakdowns happen. This leads to improved uptime and operational resilience.
3. What is IoT-based predictive maintenance in the manufacturing sector?
IoT-based predictive maintenance involves connecting machines to sensors that collect data on temperature, vibration, pressure, and more. This data is continuously streamed into a central system like ServiceNow, where it’s analyzed for signs of wear or failure. It allows manufacturers to monitor equipment remotely, spot issues early, and schedule maintenance with minimal disruption.
4. What is the main benefit of using a predictive maintenance approach for manufacturing machinery?
The biggest advantage is significantly reduced unplanned downtime — often by 30–40%. Predictive maintenance also helps lower maintenance costs, extend equipment lifespan, improve safety, and boost technician productivity. It transforms maintenance from a reactive cost center into a strategic enabler of efficiency and resilience.